Precision in ECU Data Logging & Analysis
Real-time collection of ECU data is vital for early fault detection and system optimisation. By capturing live parameters (such as engine RPM, throttle position, and sensor readings), engineers can proactively monitor systems and detect anomalies before they escalate. This data-driven approach allows for fine-tuning of engine and control algorithms, leading to improved efficiency and safety.
Hadfield Services provides advanced data logging solutions tailored for both automotive and industrial control systems. Their logging platforms interface with standard vehicle communication buses (CAN, FlexRay, LIN, etc.), capturing comprehensive, fully traceable datasets for in-depth analysis and rapid fault diagnosis.
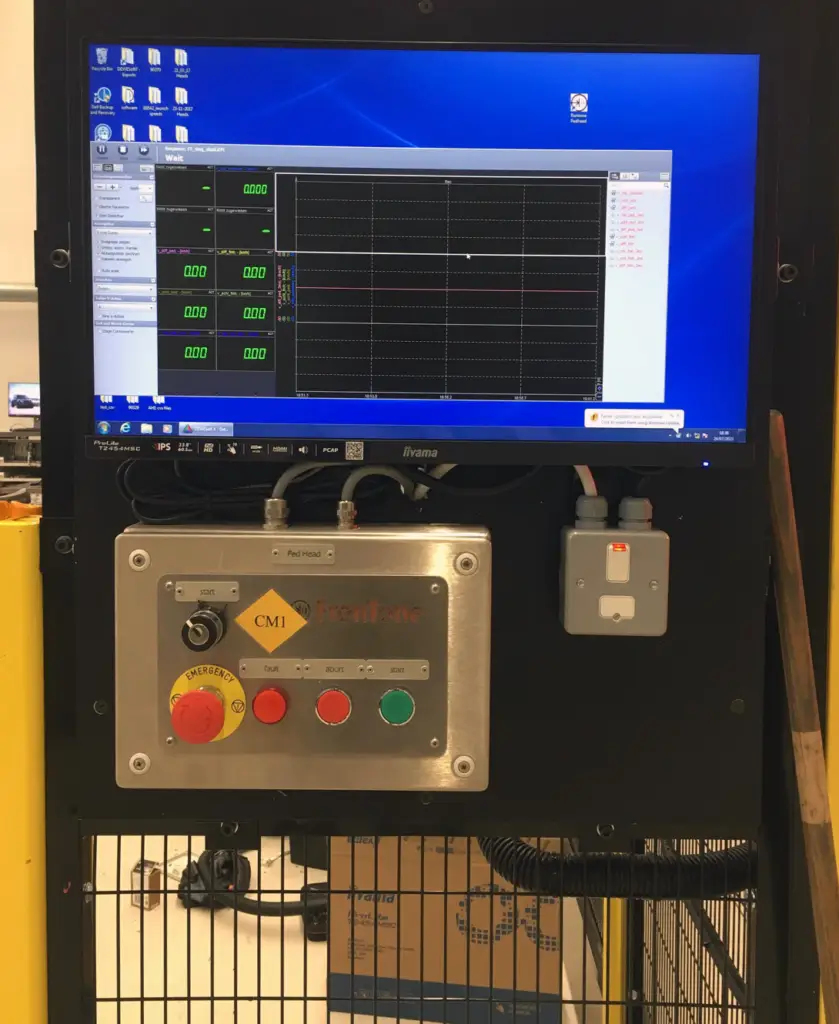
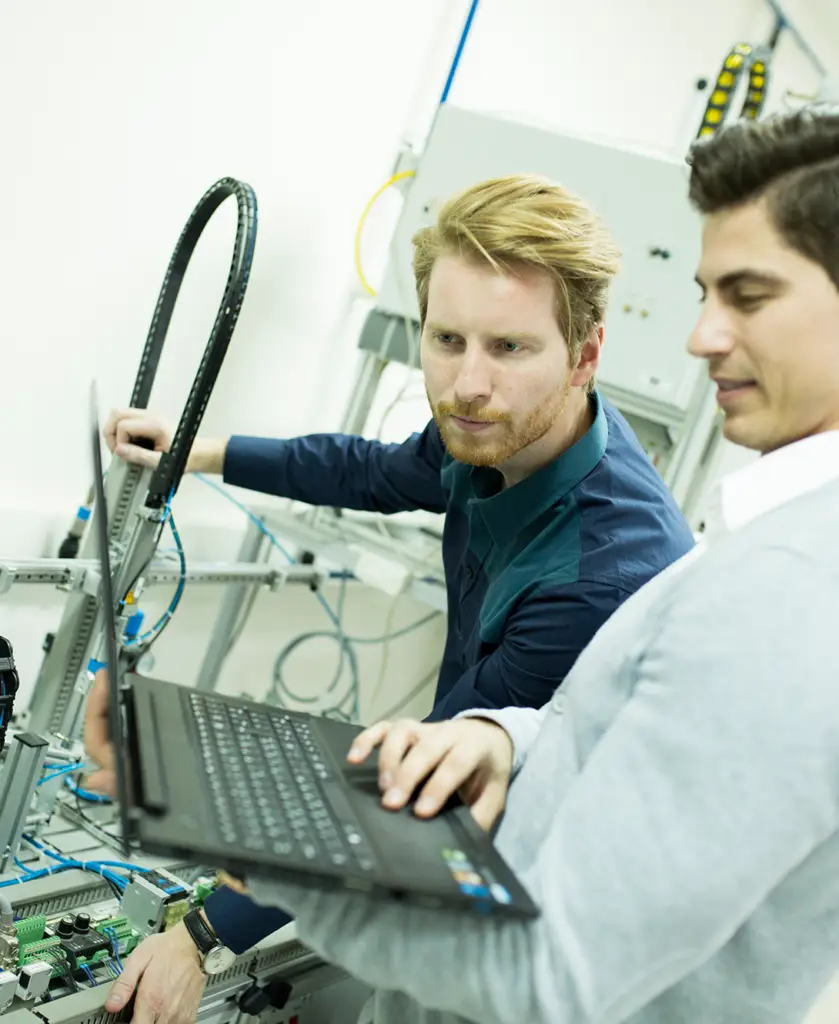
Automated Testing for Compliance & Performance
In regulated industries, automated testing streamlines compliance verification and ensures consistent ECU performance. Complex test scenarios ā from automotive emission cycles to aerospace safety checks ā can be executed automatically, guaranteeing that every requirement is validated under controlled conditions. These automated test environments run procedures with exacting repeatability, eliminating variability and greatly reducing the chance of human error. By leveraging automated testing frameworks, engineers can streamline the process, minimise manual errors, and complete test cycles much faster.
The efficiency of automation not only improves test coverage but also accelerates time-to-market, as ECUs can be verified against regulatory standards (e.g. functional safety or emissions regulations) and performance benchmarks more quickly. Moreover, each test run generates detailed logs and reports, providing an audit trail to demonstrate compliance to certifying authorities.
Advanced Testing Protocols
Hadfield Services delivers tailored ECU test systems for different applications, recognising that each project ā whether an automotive powertrain ECU, an industrial machine controller, or an aerospace flight control unit ā has unique requirements.
Every custom test rig and protocol is designed to simulate the ECUās real operating environment and stress conditions, ensuring that potential failure modes are identified and mitigated during development. This rigorous approach results in robust and reliable ECUs that perform consistently in the field.
hardware-in-the-loop (HIL) simulations
To further guarantee reliability, Hadfield Services integrates hardware-in-the-loop (HIL) simulations into its testing protocols. HIL testing connects real ECU hardware with simulated vehicles or machinery, allowing engineers to verify ECU performance against real-world scenarios using digital twins of the systemā.
This approach enables continuous, around-the-clock validation of an ECUās behaviour without the need for costly physical prototypes, effectively providing automated 24/7 test coverageā.
a significant acceleration in development cycles
The result is a significant acceleration in development cycles and increased confidence in safety margins, since ECUs can be stressed under thousands of conditions in a virtual environment. In aerospace applications, for instance, HIL setups can cost-effectively run flight-critical ECUs through complex scenariosāĀ that would be impractical or risky to recreate in live flight tests, thereby improving test safety and overall system reliabilityā.
Through these advanced testing protocols and tools, Hadfield Services ensures that every ECU it works with is validated thoroughly ā delivering proven reliability and performance.