The automotive industry is undergoing a seismic transformation, driven by electrification, autonomous vehicles, and connectivity. At the heart of these advancements lies electromechanical prototypingāa critical stage in the design and development process that ensures reliability, safety, and performance. As a leader in bespoke engineering solutions, Hadfield Services Ltd (HSL) applies its expertise in prototyping to deliver innovative and precise designs for its automotive clients. This article explores industry best practices and how HSL integrates them to redefine reliability.
The Growing Complexity of Automotive Systems
According to a report by Market Research Future, the automotive 3D printing market is projected to grow from USD 2.97 billion in 2022 to USD 9.7 billion by 2030, exhibiting a compound annual growth rate (CAGR) of 15.94% during the forecast period.
This growth is driven by the increasing demand for rapid prototyping and the development of complex automotive components. Companies like HSL are at the forefront of this evolution, leveraging advanced prototyping techniques to deliver innovative and reliable solutions in the automotive sector.
By integrating advanced technologies and adhering to industry best practices, HSL ensures that their prototypes meet the rigorous standards required in today’s automotive landscape. Our commitment to excellence not only contributes to the advancement of vehicle technology but also supports the industry’s shift towards more efficient and sustainable transportation solutions.
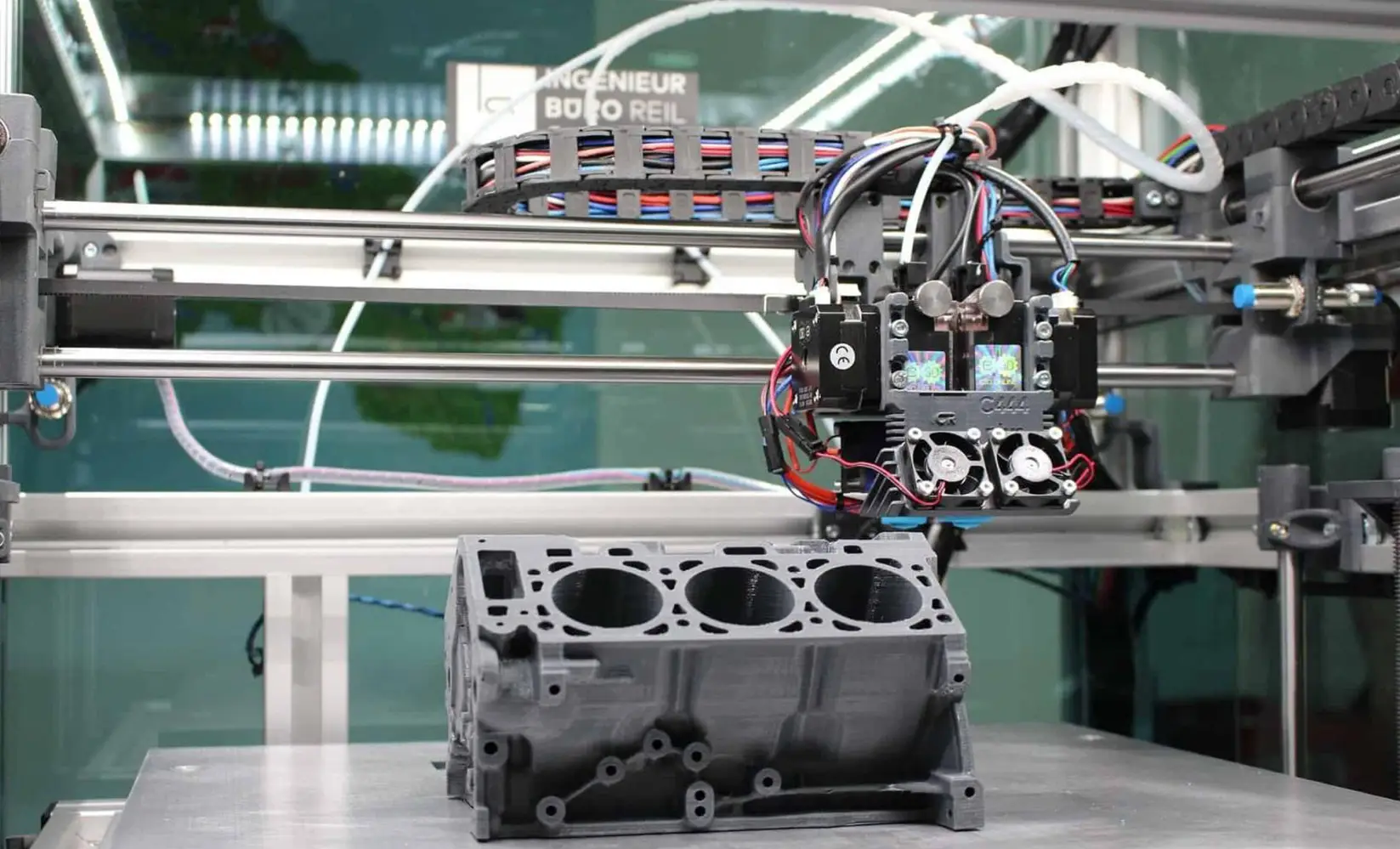
The Importance of Prototyping in Automotive Innovation
Electromechanical prototyping serves as the foundation for modern automotive design, allowing engineers to test and refine concepts before full-scale production. Companies like Hadfield Services LtdĀ are leading the charge, utilising advanced prototyping techniques to enhance the reliability of electrical systems and mechanical components.
HSL has gained recognition for its ability to address challenges in the automotive sector, particularly in the design and manufacture of bespoke harnesses and test rigs. Our innovative approach ensures that prototypes meet stringent safety and performance standards, helping clients achieve shorter development cycles and improved product reliability.
As the automotive industry continues to evolve, electromechanical prototyping will play an increasingly vital role.
Emerging Trends in Prototyping Technology
Additive Manufacturing (3D Printing): The adoption of 3D printing has revolutionised prototyping by enabling the rapid production of complex components. This technology not only reduces lead times but also allows for cost-effective iterations during the design phase. A study from Allied Market Research highlights how 3D printing is becoming integral to automotive development, with growing demand for custom and precision parts.
Digital Twin Technology: Digital twins simulate real-world scenarios, offering valuable insights into how a prototype will perform under specific conditions. By integrating digital twin systems, manufacturers can identify potential issues early, saving time and resources during the development process.
Advanced Materials: Prototyping now includes the use of lightweight, high-strength materials such as carbon fibre composites and advanced polymers. These materials align with the industryās focus on fuel efficiency and sustainability.
IoT-Enabled Testing: Internet of Things (IoT) integration enables real-time data collection during prototype testing. This approach enhances predictive maintenance capabilities and ensures optimal system performance.
Best Practices for Reliable Prototyping
To achieve success in electromechanical prototyping, manufacturers must adhere to several best practices:
- Collaboration Across Teams: Prototyping requires seamless communication between design, engineering, and manufacturing teams. This collaboration ensures that prototypes align with project specifications and client expectations.
- Iterative Testing: Continuous testing during the prototyping phase allows manufacturers to identify and resolve design flaws early. HSLās custom test rigs exemplify this approach, providing precise diagnostics to validate component performance.
- Focus on Sustainability: Incorporating sustainable practices into prototyping is critical. HSL has embraced initiatives like recycling waste materials and optimising energy use in their operations, reflecting the industry’s broader push toward greener manufacturing.
- Precision Engineering: High-precision tools and processes are essential for ensuring prototypes meet exacting automotive standards. HSL leverages advanced technologies such as heat-controlled tools for harness production, ensuring accuracy and reliability.
For media inquiries or more information, please contact Hadfield Services Ltd atĀ [email protected].
What do you think?
It’s inspiring to see how companies like HSL are pushing the boundaries to create dependable solutions in such a demanding field. Truly, this is the direction the future of automotive engineering needs to take!